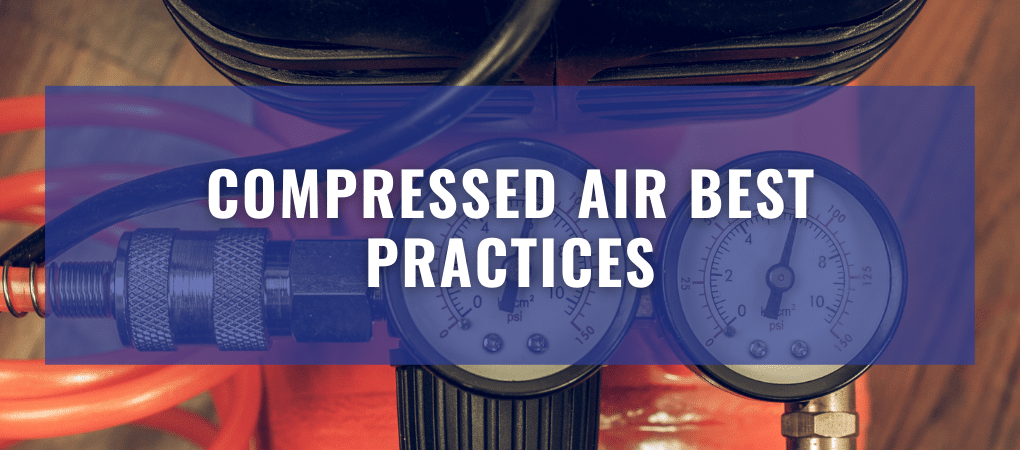
Compressed Air Best Practices
For compressed air best practices, people must understand everything about it. Compressed air is the air that is kept under higher pressure than the normal atmospheric pressure. It is an important medium of transferring energy in several industrial processes and power tools.
Uses Of Compressed Air
• Inflating pool tubes and car tiers.
• Spray painting.
• Pressure washing.
• Scuba diving.
• To power compactors, drills, and hammers in construction.
• To power sprayers, tractors, and pumps in agriculture.
• For cooling and heating in car engines.
• HVAC (Heating, Ventilation, and Air Conditioning).
How To Use
To implement compressed air best practices, people must understand how to use it properly. Sometimes, the instructions are on the manufacturers’ packaging, but there are some general ways to use compressed air.
Evaluate Application Needs
There are numerous ways people can use compressed air, and for proper use, people have to understand why they need them. That not only helps them get the best out of their compressors but also helps reduce operating costs.
People should record when they use air compressors and how much pressure they use each time. They should also document their peaks and lows to determine the most pressure and slightest pressure they use.
They should also understand what exactly the air compressor will be used for. That will help them purchase a suitable compressor that will meet their needs as intended.
Purchasing the best air compressor according to application needs
Air compressors come in different sizes and styles, all suited for different application needs. To properly use an air compressor, users should always ensure that they buy those that suit their needs.
For example, if they are being used where air needs to remain free of contamination, oil-free scroll compressors are the best. Also, if used for commercial purposes, they need to be bigger than those used for personal use.
People should educate themselves on the different air compressor models and their features and see if they will help them attain their application goals. They can do that by asking for advice from experts around them.
Understand Operation Cost
Air compressors, just like other machinery, need money to run. Buying the air compressor is just the beginning of the overall cost. Using compressed air every day is where the actual costs come in because it needs to be used continuously to ensure productivity.
Their use can account for around 30% of the total electricity bill, which can be a lot! Therefore, users have to do everything possible to monitor their usage.
When it is not in use, it is best to have the compressor turned off. That helps reduce cost. The best way to ensure that it never runs when the compressed air is not being used is to have automatic controls.
Anytime when using air compressors, the uses should use the minimum number needed for any application. They should also use the minimum level of pressure that can be used for any application.
Air leaks are another way that the costs of using air compressors can increase. Not only do they slow down production, but they also waste a lot of air that will be paid for.
Check For Leaks
As we mentioned, leaks can be costly; people must understand where and how to check them. The easiest way to spot leaks is by listening for hissing sounds. People could also use ultrasonic acoustic detectors if they are in a noisy place.
Some of the significant places that leaks can occur include:
• Regulators.
• Overhead distribution.
• Filters.
• Hose fittings or connections.
• Line lubricators.
• Ground-level air hoses.
• Quick couplers.
Leaks must be closed off as soon as they are identified.
Use air compressors for intended purposes only
Using an air compressor for anything other than what it was intended to do can increase the amount of compressed air being used, increasing cost. It could also lead to severe injuries or death.
Ensure Proper Installation
How and where air compressors are installed can make a big difference in operating, power consumption, and safety. It can also play a massive part in reducing the risk of leaks.
How To Install Air Compressors
Air compressors should be installed as far away from other machinery as possible, primarily if they emit heat. They should also be put in a cool, dry, clean, and adequately ventilated room because humidity may cause them to rust.
The air entering the air compressor should also be consistent, clean, dry, calm, and free of any impurities. People should have their air compressors installed as close to where they will be used as possible because placing them far away reduces their efficiency and increases chances for leakages.
Some tips for proper installation include;
• The air compressor should be installed horizontally on a solid flat floor.
• Install cable glands that protect electrical wires and prevent dust from penetrating.
• Ensure there is enough space around the air compressor. That comes in handy during maintenance.
• Use the proper fuses and ensure that the main switch has an allowance for a tag or lockout protocol.
How To Ensure Air Compressors Are Being Used Properly
Installing an air compressor does not always mean that it is being used correctly. There are some things that users can do to ensure that the compressors are being used properly.
Ensure Optimum Operating Temperature
High temperature is one of the major things that cause a lot of machinery to fail. High temperatures could cause an air compressor to explode.
For optimum temperature, the water temperatures should be 100F above inlet air temperature. Cooling water outlet temperatures must not be more than 490F.
Ensure Proper Lubrication
Lubricating air compressors is key to maintain effectiveness, and they should be lubricated using a lubricant that is suited for the services the compressor provides.
Clean the Air Filter
Air filters keep the air clean, which is why they must also be free of any dust and debris.
Clean Intake Valves
Intake valves are where air enters the compressors, and if they are dirty, the air will also be dirty.
Adjust Belt Tension
Belt tension ensures proper operation of the compressor. Old belts should also be replaced to avoid wearing out during operations.
One must buy from the best dealers for the best air compressors, which is why Air Power Equipment Co. is here. They not only sell you the best air compressors but also carry out maintenance for used air compressors.
They have different air compressors’ types and sizes to ensure that all their clients’ needs are met.
Air Power Equipment Company in Oklahoma City (OKC), is the leading source for new air compressor sales and used air compressor sales throughout the country. We specialize in rotary screw air compressor sales and reciprocal air compressor sales. Air Power Equipment Company is also the best source for air compressor service and air compressor parts in Oklahoma. If you are looking for new air compressors, used air compressors, air compressor parts, or air compressor service call Air Power Equipment Company OKC. We are experts with all brands of air compressor equipment and we are a stocking distributor of air compressor brands like FS Curtis Air Compressors, Champion Air Compressors, Campbell Hausfeld Air Compressors, Kellogg Air Compressors, American Air Compressors, Quincy Compressor and many more. Call us at (405) 445-1216 – we have what you need, and at the best price you will find.